Combining the Science of Stability and Seakeeping
Working with a leading classification society, two Naval Architecture and Marine Engineering students developed a straightforward methodology to help design plan appraisal surveyors assess the likelihood of a loss of ship propulsion when high waves cause ships to incline at high angles.
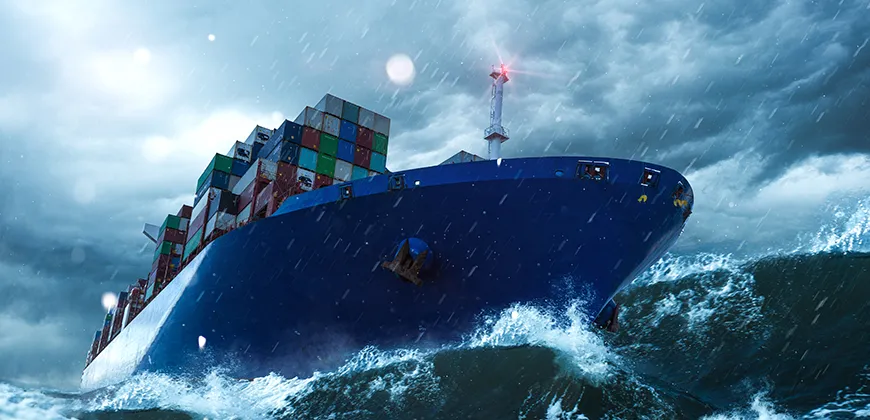
When seas are rough, rolling and pitching waves can push ships to inclines at which marine engine failure is a real possibility. Disasters can happen, as has been seen from several high-profile accidents. In 2015 in the midst of Hurricane Joaquin, the cargo ship S.S. El Faro listed at an angle that caused the sump to lose suction. The engines failed, the ship sank and all 33 people on board perished at sea. In 2019, the cruise ship Viking Sky listed at high angles, suffering a loss of oil pressure that shut down all engines and required evacuating hundreds of passengers by helicopter. Cargo ships that travelled to help with the rescue operation also experienced engine failure.
Global classification societies are keenly interested in learning more about what causes these types of incidents and developing tools to identify and prevent potential issues before they lead to disaster.
In the summer of 2021, Anthony Brandon and Pezhman Ghalich, two students in the Master of Engineering Leadership (MEL) in Naval Architecture and Engineering, joined forces to address this very issue. Working with a classification society, they developed a design plan appraisal methodology that is consistent with existing maritime rules, regulations and guidelines. This methodology can be used by design plan appraisal surveyors to predict the inclination of a ship at sea over its lifetime and better understand the maximum inclines and associated accelerations under which engines and auxiliary machinery can safely operate.
“Ships are rolling and pitching at sea all the time,” says Anthony. “At certain inclinations, a lack of lubrication oil, fuel or cool water suction can cause a crash stop where you lose propulsion entirely.”
The two began their study by using the S.S. El Faro as a test case to calculate the motions that a ship might experience in a range of conditions over its lifespan. They did this using Maxsurf Motions, an integrated seakeeping analysis and motion prediction module used to calculate a ship’s movements in irregular waves. The analysis took into account loading conditions, wave environment, ship speed and wave headings.
From these calculations, they then produced scatter heat plots showing the probability of various inclinations, as well as the associated accelerations that could result in a dead ship and loss of propulsion.
Their study also reviewed the current rules relating to dynamic inclination for marine diesel engines and auxiliary machinery. The SOLAS II-I Part C regulation requires that propulsion machinery and all auxiliary machinery deemed essential to the propulsion and safety of the ship must be designed to operate when the ship is “inclined at any angle of list up to and including 15° either way under static conditions and 22.5° under dynamic conditions (rolling) either way and simultaneously including dynamically (pitching) 7.5° by bow or stern.”
However, as they state in their summary report, Anthony and Pezhman discovered that neither the International Association of Classification Societies requirements for machinery installations nor the classification society’s test specification “contains a period for the dynamic pitch and roll…in other words, the dynamic inclination tests are in fact static.”
“We found that engines might be designed to withstand a 22.5 degree of dynamic inclination, but they are not dynamically tested at that incline,” says Anthony. “The ships are certified as good to go, but when they are out at sea they may be cutting out at lower angles.”
Importantly, their methodology takes into account not just inclination – as is done under current regulations – but acceleration as well. “I have experienced 24 degrees of inclination in my job at sea, but the acceleration of that inclination and its duration is as important to take into account in ship design,” says Pezhman.
The two hope that the methodology they developed will eventually provide an efficient and cost-effective way for design plan appraisal surveyors to identify the conditions within which marine diesel engines and all auxiliary machinery are to be capable of operating.
Looking ahead, the two propose that the next step would be to acquire and model a common hull form, and then scale the model for various lengths so that surveyors could then use the scatter heat plots when reviewing design plans. This would make it relatively easy for the ship surveyors to determine the probability that a ship might roll to an inclination significant enough to require a redesign.
Anthony and Pezhman say that their work on this project encapsulates the spirit of both the MEL and the Naval Architecture and Marine Engineering program.
“Pezhman has worked on ships as a marine engineer on oil tankers for more than five years while I have been hands-on in my career on the design and approval side,” says Anthony. “This project puts the two together, and is a fantastic example of why it’s so valuable to move beyond those silos to bring people together from different backgrounds to try and address some of the industry’s most significant challenges.”