Evaluating the feasibility of green ammonia production
As part of their Venture Design Lab course, Sustainable Process Engineering students evaluate the technical and economic viability of a new sustainable process or product. Barry Kanchan looked at the feasibility of producing green hydrogen as a feedstock for a currently idled ammonia plant in Trinidad & Tobago.
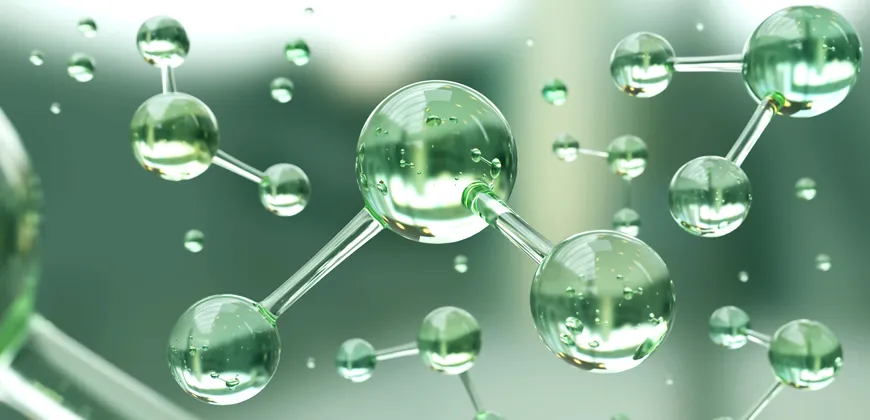
In the Venture Design Lab, a required course in the Master of Engineering Leadership (MEL) in Sustainable Process Engineering program, students develop a commercialization plan for a sustainable product or manufacturing process. For Barry Kanchan, who has numerous years of experience in his home country’s oil and gas industry, this represented an opportunity to consider the viability of using feedstocks other than natural gas to fuel the country’s industrial sector.
Facing dramatic declines in its natural gas production, Trinidad & Tobago is exploring ways to diversify its economy and industrial sector, which includes 16 ammonia and methanol plants that produce around three percent and nine percent, respectively, of the world’s total ammonia and methanol production.
“Trinidad’s ammonia plants rely on natural gas as a feedstock for hydrogen, and my idea was to replace that feedstock with green hydrogen produced through solar energy that then powers an electrolyzer that generates hydrogen for the ammonia plant,” explains Barry. “My project was basically a technical and economic analysis of a new technology development cycle.”
He notes that his proposed technology chain includes six elements, of which four are already in service in the country’s chemical industry. “Integrating these six technologies allows for the production and use of clean hydrogen, which can be used as a feedstock to produce green ammonia to make fertilizer and other products.”

Barry applied a standard techo-economic analysis methodology to evaluate the viability of the integrated green ammonia production chain. He compared this against a base case of producing hydrogen through steam methane reformation of natural gas followed by carbon capture and sequestration. He included capital and operational cost estimates for developing the solar farm and electrolyzer; explored scenario sensitivities for capital costs and prices for electricity, hydrogen and carbon; and identified key risks and potential strategies for mitigating those risks.
Barry’s analysis found that the life-cycle cost of hydrogen for the integrated solar farm and electrolyzer investment is getting much closer to the cost per kilogram of hydrogen when produced through steam methane reforming.
“It wasn’t surprising to me that steam methane reforming is less expensive than the sustainable alternative I was examining,” says Barry. “However, the life-cycle costs of renewable energy generation have declined significantly in recent years. If they continue to do so, it could enable projects like this to compete economically. Similarly, if the market for green products continues to grow, agricultural producers could begin demanding fertilizers made through green production processes, for which they might be willing to pay a premium.”
Barry says he was attracted to the MEL in Sustainable Process Engineering because he wanted to expand his career into sustainable energy. “I saw that the MEL offered this content from both an engineering and business perspective and I believed it could provide me with the knowledge, skills and professional network to make this transition.”
He says that the integrated analysis he undertook as part of the Venture Design Lab was a very worthwhile experience. “It helped me think about how new technologies or processes can be used to produce commodities like ammonia,” he says. “I also believe this type of analysis could be of benefit to Trinidad & Tobago as it seeks projects to diversify the economy as well as to large corporations who are interested in developing green products to meet growing market demand.”